Flow Meter Services
Accurate Flow Measurement is critical to determine the amount of material purchased and sold. Flow rate is determined by installing a flow meter, which uses flow-through calculations to measure the liquid’s flow, volume, speed or mass. Both gas and liquid flow can be measured in volumetric or mass flow rates, such as litres per second or kilograms per second. In the chemical industry, flows throughout the process need to be regulated to desired values, requiring very accurate measurements of the liquid’s flow mass or volume.
Floweigh provides complete, fully accredited calibration services for all of your liquid flow calibration needs using the latest technology and expert technicians. Our liquid flow calibration services can be customized to meet any of your specific calibration requirements.
Quick, Quality Repairs. Qualified repairs and reconditioning of flow metering and controlling instruments are available. While spare parts are stocked for many lines, Floweigh has established relationships with many manufacturers, which enables us to obtain many additional parts and get you back in production. Because of our history of experience and building great customer and vendor relationships, Floweigh is able to complete your repairs quickly, while maintaining our standard of quality service.
Liquid Flow Meters
When choosing your flowmeters, consider such intangible factors as familiarity of plant personnel, their experience with calibration and maintenance, spare parts availability and mean time between failure history at the particular plant site.
To avoid flow measurement mistakes and costly reinstallations, it’s recommended that the installation costs be computed only after taking these steps.
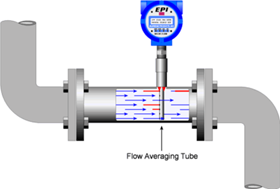
Flow Averaging Tube
Flow Meter Selection
To select the best flow meter for your specific needs, It’s necessary to invest time in fully evaluating the nature of the process fluid and overall installation.
- Should flowrate info be continuous or totalized?
- Is information needed locally or remotely?
- If remotely, do you require analog, digital
or shared? - If shared, what is the required minimum data-update frequency?
- Fluid Properties and Flow Characteristics:
pressure, temperature, allowable pressure drop, density (or gravity), conductivity, viscosity, vapor pressure, how properties might vary or interact, safety or toxicity, presence of bubbles or solids, tendency to coat, and light transmission qualities (opaque, translucent, or transparent) - Piping and Environmental Factors:
direction (avoiding downward flows), size, material, schedule, flange-pressure rating, accessibility, regulators, valves, up or downstream turns, and straight-pipe run lengths. - Presence of vibration or magnetic fields?
- Does it require sanitary or clean-in-place compliance?
- Is area classified for explosion hazards?
- Determine required meter range (mininum/maximum flows)
- Determine required flow measurement accuracy: the % of actual reading (AR), calibrated span (CS) or full scale (FS).
- State accuracy requirements separately for minimum, normal and maximum flowrates.
Types of Flow Meters
Due to the wide applications and types of liquids, there is no single metering technology that is best for all applications. Factors that influence liquid flow rate include the liquid’s speed, volume, viscosity, temperature and density, as well as the friction of the liquid in contact with the pipe.
Flowmeter Classifications
Based on historical introduction and performances in accuracy and product lifetime,, flowmeters are broadly classified between “new technology” and “traditional technology” flowmeters.
Traditional Flowmeters — were introduced before 1950 and have less focus on product development. They are subject to wear, are less accurate than “new-tech” flowmeters and require more maintenance. In spite of these problems, the traditional market is holding strong.
New Technology Flowmeters — were introduced after 1950 and are eager to incorporate newer technologies to solve typical flowmeter problems. They offer increased accuracy and reduced wear.
Traditional Technology Flowmeters
- Differential Pressure (DP)
- Open Channel
- Positive Displacement
- Turbine
- Variable Area
New Technology Flowmeters
- Coriolis – 1977*
- Magnetic – 1952*
- Multi-variable Differential Pressure (DP) – 1992*
- Thermal
- Ultrasonic – 1963*
- Vortex – 1969*
* Year introduced.
Magnetic Meters
Magnetic flowmeters are used primarily to measure the flow of conductive liquids or slurries (like paper pulp slurries). Although magnetic flowmeters is initially higher than positive displacement and turbine flowmeters, they are more accurate and do not generate pressure drop. Since they measure “conductive” liquids, their main limitation is that they do not measure “non-conductive” liquids (hydrocarbons) for the oil, gas and refining industries.
Differential Pressure Meters
The main parts in a differential pressure device are orifices, venturi tubes, flow tubes, flow nozzles, pilot tubes, elbow-tap meters, target meters and variable area meters. [Watch video for more details.]
Bulk Delivery Truck Meters and Bulk Tank Meters
Bulk flowmeters are commonly used on retail tank trucks or on truck loading racks for high speed fueling. Using reliable, low-maintenance bulk flow meters will provide lower overall costs for you.
Have Special Bulk Tank Meter Needs?
Floweigh can assist in selecting the most desirable features to solve your bulk tank loading, unloading and flow measurement needs. Some issues we’ve solved for other customers included “bulk tanker loading terminals for tank truck filling and storage facilities where moving product between tanks must be measured (especially important when custody transfer was involved).”
Positive Displacement Meters
Positive displace-ment flowmeters include piston, oval-gear, nutating disk (wobble plate) and rotary-vane types. In a positive displacement meter, the fluid is separated into individual volumetric elements and the numbers of elements per unit time are measured by the sensors.
Operating positive displacement units consists of separating liquids into accurately measured increments and moving them forward. Each segment is counted by a connecting register and, because every increment represents a discrete volume, positive-displacement units are popular for automatic batching and accounting applications.
Velocity Meters
A Velocity meter has turbine, vortex shedding, electromagnetic and sonic designs. Velocity meters operate linearly with respect to the volume flow rate. Their rangeability is also greater because there is no square-root relationship (as with differential pressure devices). Most velocity-type meter housings have flanges or fittings that allow them to be connected directly into the pipelines.
Mass Meters
Mass meters consist of Coriolis and thermal types. Due to the need of increased accuracy of flow measurements in mass-related processes (such as chemical reactions and heat transfer), new developments were necessary in mass flowmeters. While various designs are available, one is most commonly used for liquid flow applications: theCoriolis meter. Its operation is based on the natural phenomenon called the Coriolis force.
Additional Resources
Coriolis Mass Flowmeters for Measuring Bulk Condensate in Gas Industry
Pipeline & Gas Journal, July 2010
The production of natural gas liquids (NGL) creates a byproduct called “condensate.” When there are variations in the hydrocarbon constituents and fluid vapr pressures, the measurement integrity can become compromised. Article discusses best practices and challenges of the measurement of liquid hydrocarbons, by addressing the benefits of Coriolis mass flowmeter measurements, viscosity challenges, diagnostics, tube damping, traceable verification, accuracy, repeatability and refinement of separator operations.